AQUASEAL Qatar elige la tecnología de mezcla y sistemas de EIRICH
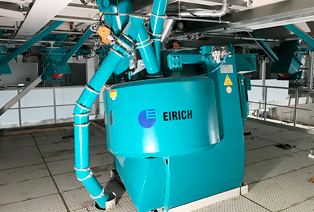
In Doha, Qatar, AQUASEAL produces dry mortar products for all phases of construction, from foundations to finishes, under the product brand name DURABUILD. The aim is to produce products that are of the highest standard. Part of the company’s strategy is to use the best production technology available on the international market. Which is why AQUASEAL chose EIRICH for the mixing and systems technology for the expansion of its production.
AQUASEAL’s product program, which is unusually wide for a producer of dry mortar products, includes adhesives, sealant and grouts; damp-proofing and water proofing protection; curing and release agents; flooring systems; coating; roof sealant and products for concrete repair and protection. Of critical importance for the quality of these materials is the mixing technology used, with the mixer being the core component of a dry mortar production plant. Single or twin-shaft mixers are supplied by a wide range of manufacturers all over the world. For high-quality products, however, the mixing technology has to meet requirements that simple systems are not capable of meeting.
This is where the advantages of mixing and systems technology from EIRICH, which come down to design, come into their own. Whereas in the “simple” mixers the vessel is stationary and the tools have to transport the material, with the EIRICH mixer the material is transported by a rotating vessel and fed to the mixing tool, called a rotor. This provides a whole host of unique selling propositions. A few of them are: The mixing tool can run fast, up to more than 30 m/s. The power input into the mix can therefore be specifically adjusted to the product. Optimum mixing and dispersing effects are achieved without choppers. With sizes from 1 to 3,000 liters, just a single rotating tool is needed, so upscaling is simple.
What advantages does this mean for AQUASEAL?
Firstly, EIRICH enables mixing qualities to be achieved that are generally beyond the reach of most other systems. In the EIRICH mixer, all the material is completely agitated in just a single revolution of the vessel. This means that the mixer mixes without demixing, which has been described as what happens in all other mixing systems. The consequence of the problems associated with “demixing during mixing” is that the mixing time has to be short. In most cases this time is not long enough to completely disintegrate agglomerates and distribute very small quantities homogeneously. Mixing for any longer, however, results in demixing effects because coarser components accumulate in the outer area of the mixing drum and finer components in the middle. This also means that the mixing times in simple mixers are dependent on the formula – sometimes shorter, sometimes longer. Not so with an EIRICH mixer: Since there is no demixing, all the formulas have the same mixing times.
For AQUASEAL there was also another reason for choosing EIRICH:
Its well-known expertise in systems engineering, combined with the capability proven many times over to design, plan and construct systems. EIRICH can call on many years of experience when it comes to dry mortar systems. For example, over the last few decades it has equipped more than 260 dry mortar plants with high-performance mixing technology and systems engineering. EIRICH aims to accommodate the specific wishes and requirements of each individual customer and to implement them to perfection, and this applies to AQUASEAL as well. Following provision of details of the formulas and the required production quantities from AQUASEAL, the complete system design and order handling was undertaken by EIRICH. The detailed engineering and the delivery encompassed silos, steel structures, conveying, feeding, weighing and mixing systems and the control systems.
The new plant, which commenced operations in autumn 2017, features a RV12 mixer (400 l size). With batch cycle times of 2-3 minutes and two-shift operations, this enables an annual production output of approx. 50,000 tons. AQUASEAL is therefore in a position to produce top-quality products with maximum efficiency.
Further information:
Contact: Volker Fitz, E-mail: volker.fitz@eirich.de